Ferobide
Introducing Ferobide, an effective and durable wear part specifically for the agricultural and mining industry.
Ferobide
Harder than rock, tougher than old boots
Ferobide - the durable tungsten carbide composite
Over 8 years ago, Tenmat Wear pioneered the development of the innovative Ferobide wear protection to address the significant limitations of traditional tungsten carbide materials frequently used on Agricultural Machinery Points.
Developed in house, Ferobide has shown positive results in field testing across a diverse range of soil conditions and machinery applications, even under the most challenging working conditions.
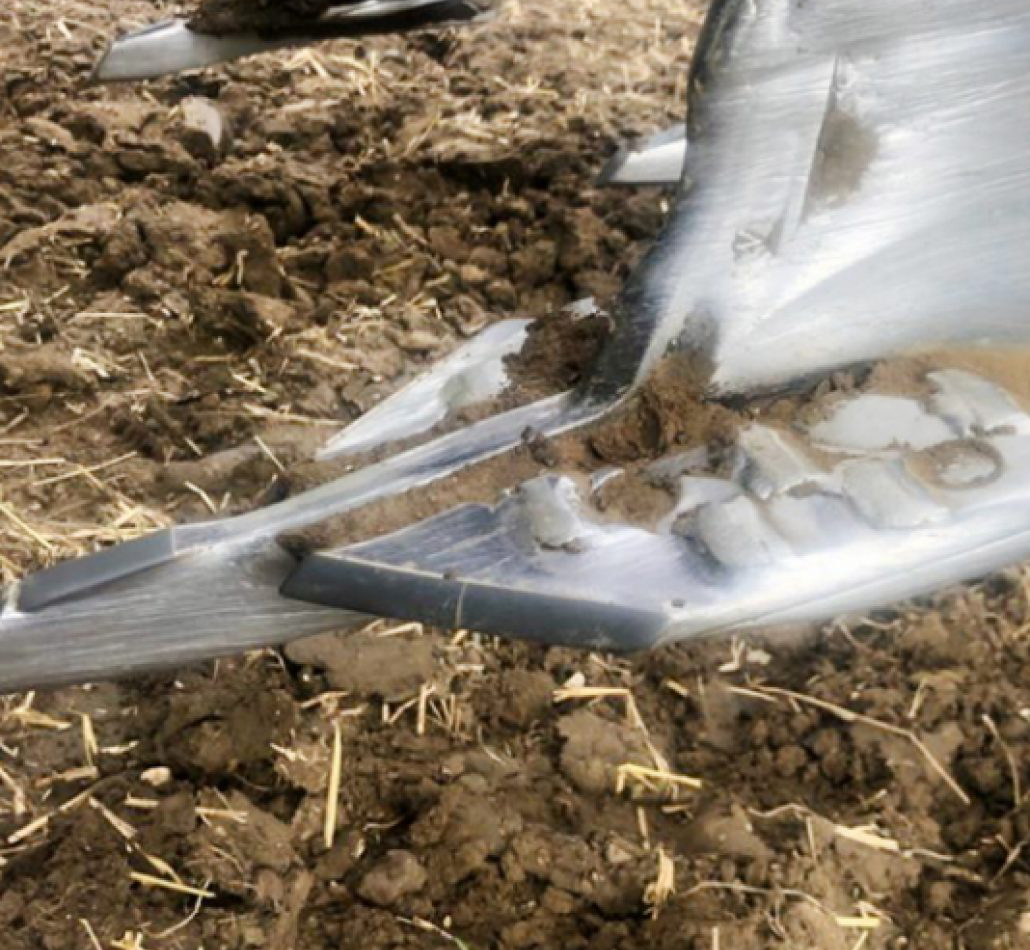
Resistance performance
Ferobide is built to withstand the toughest conditions
Distinct from traditional tungsten carbide, Ferobide employs a steel matrix to bond the tungsten particles. This unique formation process provides exceptional wear resistance, bolstered by superior impact and chipping resistance. Ferobide is composed of premium, durable tungsten carbide and boasts a hardness typically around 1500 HV.
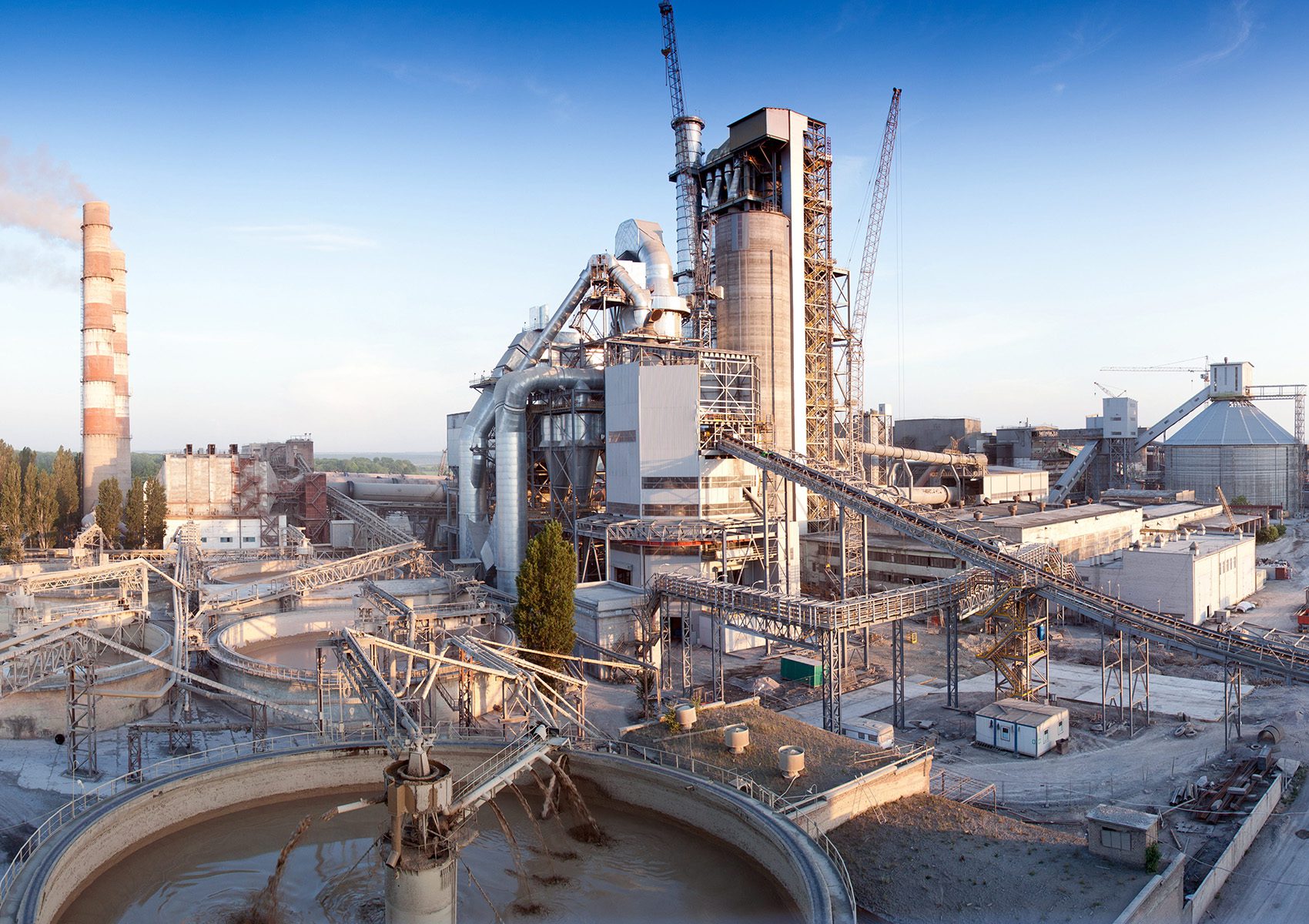
Why choose Ferobide?
No matter what soil conditions you work in, Ferobide stays strong against even the most severe abrasive conditions. Ferobide has been proven in the field as being an abrasion-resistant composite of choice that can help improve the service life of parts and equipment.
Hardness
Thanks to Ferobide’s hardness, wear is minimised.
Versatile
Whatever you need Ferobide for, you’ll find a range of grades and dimensions to suit your application.
Performance
Ferobide’s performance isn’t just at the surface level. Hardness and durability run all the way through Ferobide wear parts.
EXPLORE INDUSTRIES
Applications of Ferobide
Hard materials
In service for nearly a decade, Ferobide was initially developed to resolve the major limitations of traditional tungsten carbide materials often used on Agricultural Machinery Points.
Originally created in-house by Tenmat Wear’s technical R&D team, Ferobide has since experienced positive field testing across all types of soil and machinery application under challenging working conditions.
50+
hours of continuous ground engagement.
8x
8 times better than 500HB boron steels.
4x
4 times better than chromium carbide hard-face overlay plates.
3x
3 times better than white case iron.
INCREASING THE WORKING LIFE OF WEARING PARTS
Superior mechanical properties
Alongside its superior mechanical properties, Ferobide distinguishes itself through its quick and easy installation. Ferobide is welded directly onto wearing parts, onto positions as determined by the user. This puts full control into the hands of the welder, and allows for components to be protected exactly where needed.
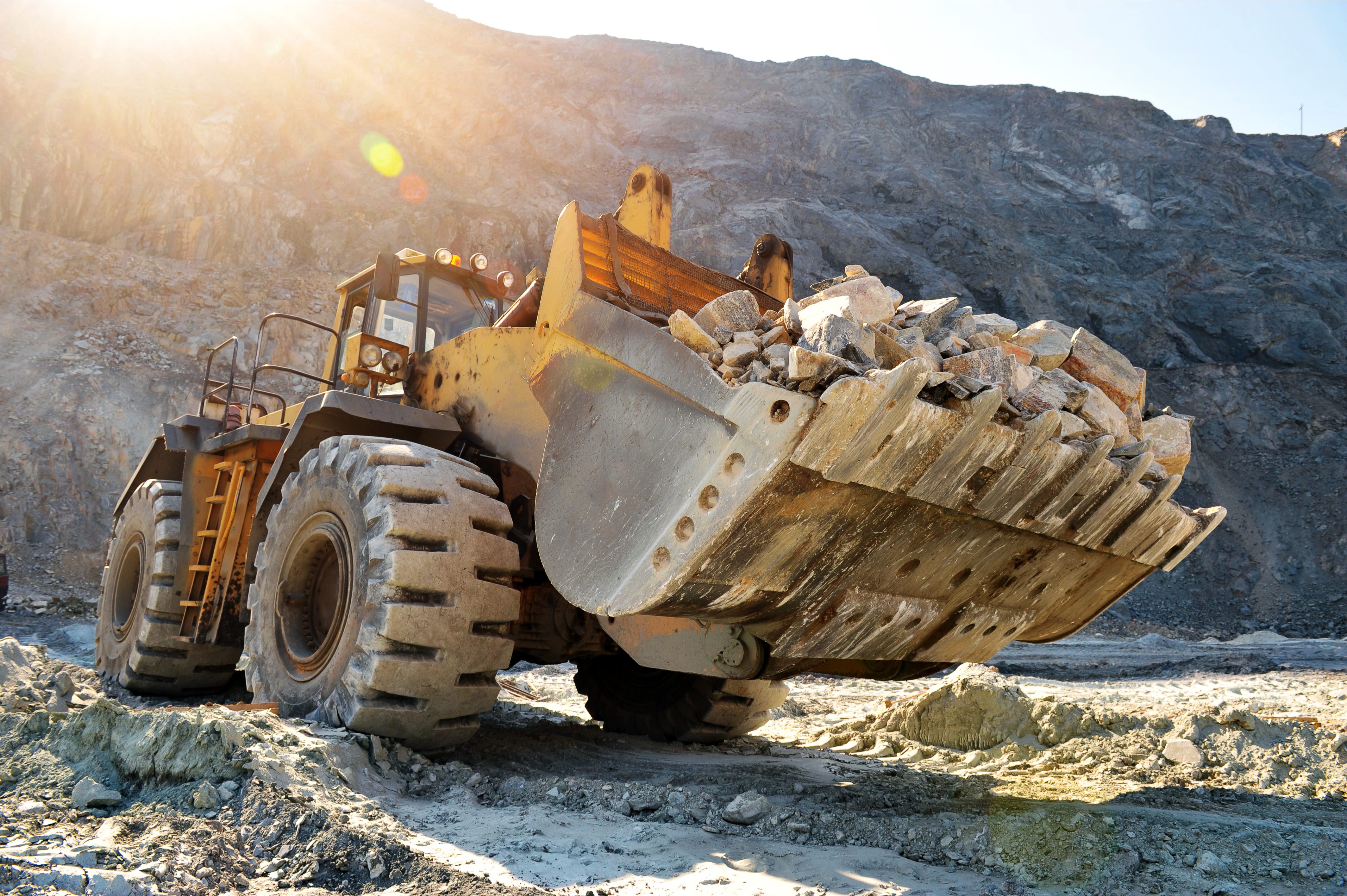
Ferobide is cut to shape with ease. This, combined with superior toughness, makes Ferobide the ideal choice for high impact and high abrasion situations. By using Ferobide wear protection, customers can significantly increase the working life of wearing parts, avoid lengthy downtime, and boost productivity.
FEROBIDE
Quality and testing
You can trust that all Ferobide parts are manufactured to high quality standards and every production batch is thoroughly checked by a team of Quality Inspectors and tested for dimensional accuracy and hardness levels. Further, samples from each batch undergo abrasive wear ASTM G65 testing to ensure consistent wear resistance.
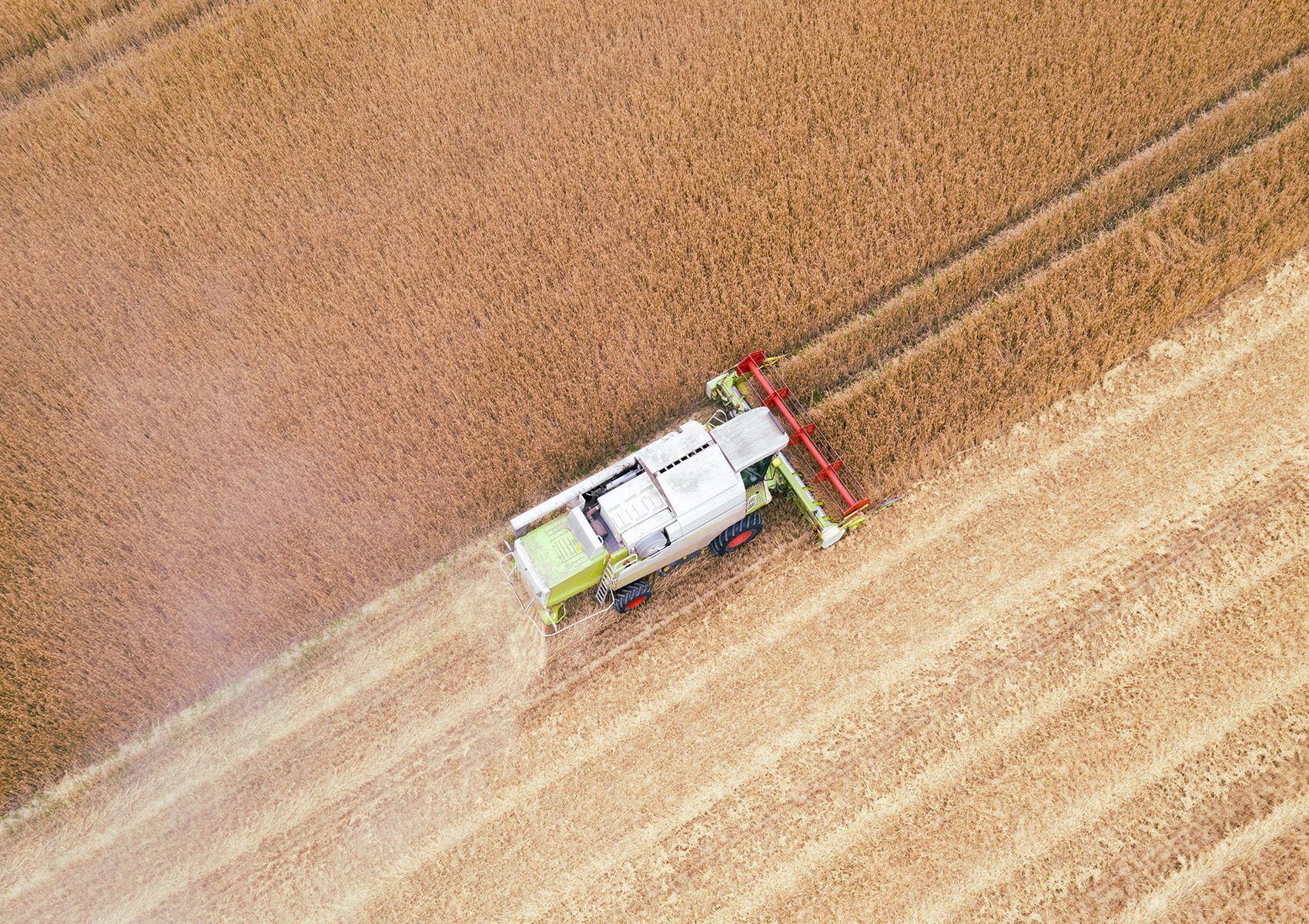
We use on-site laboratory
equipment to ensure the effectiveness of Ferobide
We also use on-site laboratory equipment to ensure that all Ferobide components have the necessary micro-structures needed to cope in the environments that they are used in.
Ferobide has more than six successful years in the field to prove real-life performance and long-term material reproducibility. Every batch of Ferobide is tested in our technical centre to maintain highest quality standards. Regular mechanical testing includes various wear testing methods.
FAQs
It is very easy and quick to weld Ferobide.
When welding Ferobide, keep heat input to a minimum, and use standard MIG / MMA methods. Clamp Ferobide in place, otherwise use a single tack per tile.
Welding gives best results for users. However, if large demand requires, Ferobide can be supplied stud-welded for screw installation. Please consult Tenmat direct for more support.
Ferobide can be used on a wide range of different machines and ground-engaging tools.
It is ideal to combat sliding wear, to prevent thinning or “washing” and is well suited for situations where brazing is not an option and hardfacing is too slow. Ferobide is typically used on seed drills, subsoilers, cultivators, ploughs, muck spreaders, root harvesters, sugar cane harvesters, buckets, mowers, augers, and scrapers.
One ideal placement is behind a brazed carbide edge, however if Ferobide is placed anywhere with sliding wear or in areas that avoid the impact of leading edges, results have demonstrated the effectiveness of Ferobide.
New developments in Ferobide have increased the impact resistance for leading edges however please avoid using standard Ferobide tiles on leading edges and points where the Ferobide is subject to heavy direct impact. Ferobide has been specially developed for excellent sliding wear performance and should only be used on leading edges with minimal impact.
Where welding is the only option for Ferobide, please enquire directly about our leading-edge solutions.
Ferobide is not to be used in above ground high speed applications, e.g. toppers, hedge flails, etc.
Ferobide is the most durable welded material readily available on the market and has upto 10x performance versus hardfacing, and up to 6x performance versus chocky blocks. Brazed pure tungsten has a slightly better wear resistance than Ferobide and while Ferobide is comparable to brazed carbide, Ferobide is slightly less durable. Brazed carbide is the best option for leading edges.
When used for the correct applications, Ferobide users can achieve a much greater working life and performance from wearing metal parts. As well as increased service life, Ferobide also helps to reduce downtime and save time & money on-farm.
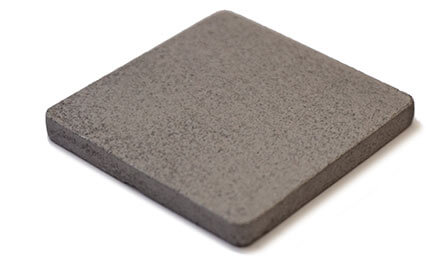
Markon Ltd.
“Ferobide is cut to shape with ease. This, combined with superior toughness, makes Ferobide the ideal choice for high impact and high abrasion situations.”
Jackson Mitchell
CMO, Markon Ltd
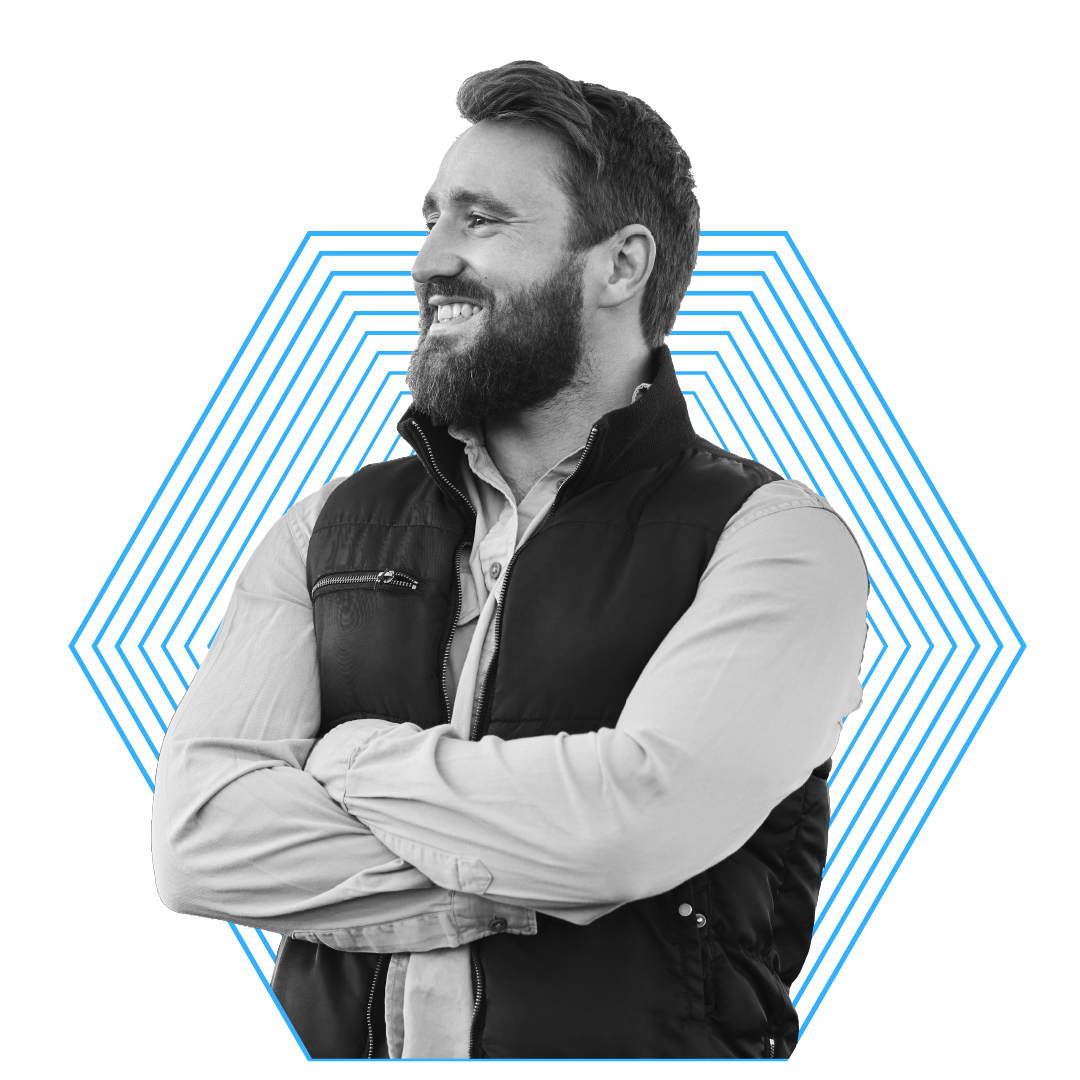
Resources
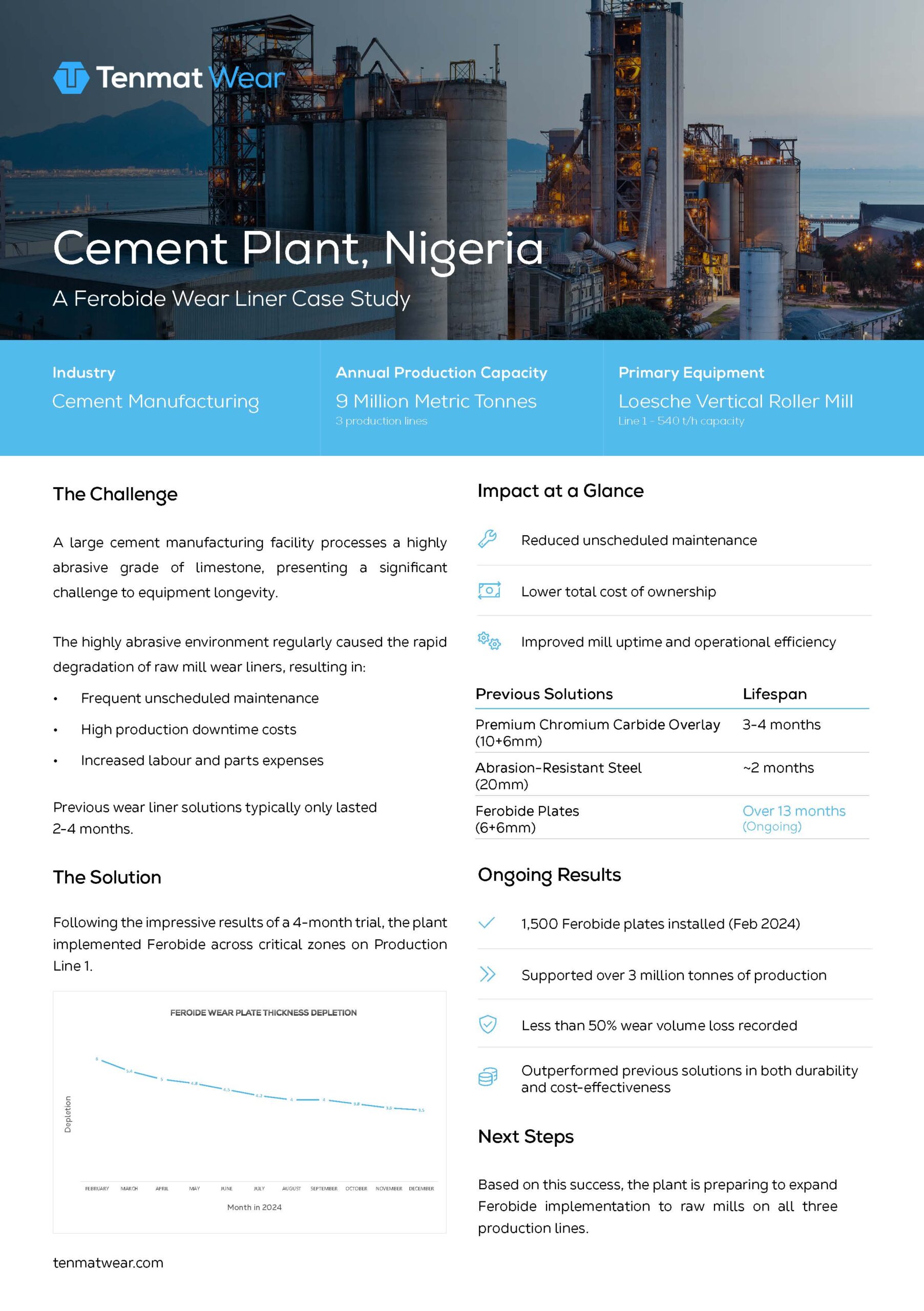
Contents
Nigerian cement plant faced rapid wear from highly abrasive limestone
Ferobide lasted 13+ months vs. 2–4 months with previous liners
Enabled 3M+ tonnes production with under 50% wear
Impressive performance driving expansion across all production lines