- Home
- Composite and Polymer Materials
- Sectors & Products
- Heavy Machinery
- Decanter Centrifuges
Decanter centrifuges
- Home
- Composite and Polymer Materials
- Sectors & Products
- Heavy Machinery
- Decanter Centrifuges
Decanter Centrifuges
Decanter Centrifuges
Superior wear protection
Decanter centrifuges are machines that separate solids from liquids using centrifugal forces. Depending on the fluid being processed, the flights of the scroll in the centrifuge can see extreme levels of wear. Only Ferobide gives OEMs a wear protection material which performs as needed without suffering the common limitations experienced with traditional materials
FEROBIDE
The ideal wear protection for decanter centrifuges
Ferobide is the ideal for decanter centrifuges, due to its easy installation via welding. Ferobide offers superior wear performance compared to hard face welding and ceramic tile options for scroll flights. The performance of a decanter centrifuge during operation is improved with Ferobide as it significantly reduces the vibration in service. Uptime hours, separation efficiency, service cycle length, and the overall lifetime are all improved thanks to Ferobide. Significant time savings are achieved due to Ferobide’s weldability during the build or repair of the decanter centrifuge.
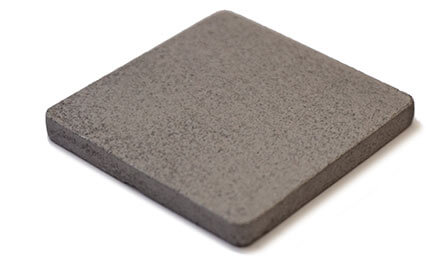
Suited to many applications
Conventional ways of protecting the flights involve the use of hard facing rods or by welding “carriers” with brazed tungsten carbide tiles.
Ferobide is also well suited for rectangular inlet and discharge ports, scrapers, and other components found on a decanter centrifuge.
Ferobide's unique strengths
Ferobide combines hardness and toughness to make it durable and crack resistant. It can also help to increase the performance and service life of parts and equipment compared to other AR steel grades.
- Significant wear resistance
Up-to 8-10 times better than typical chromium hard facing, and up-to 4 times better than typical alumina ceramics.
- Noise reduction
Significant reduction in noise and vibration levels because the scroll remains balanced through using Ferobide tiles.
- Longer service cycle
Ferobide has proven to outlast the typical service cycle for wastewater decanters.
- Reduced cost
Up-to 8-10 times better than typical chromium hard facing, and up-to 4 times better than typical alumina ceramics.
- Reduced scroll build time
Significantly reduced scroll build time when welding Ferobide compared to hard face welding.
- Fast dispatch
Standard Ferobide tiles available on stock for immediate dispatch.
FAQs
It is very easy and quick to weld Ferobide.
When welding Ferobide, keep heat input to a minimum, and use standard MIG / MMA methods. Clamp Ferobide in place, otherwise use a single tack per tile.
Welding gives best results for users. However, if large demand requires, Ferobide can be supplied stud-welded for screw installation. Please consult Tenmat Wear for more support.
Ferobide can be used on a wide range of different machines and ground-engaging tools.
It is ideal to combat sliding wear, to prevent thinning or “washing” and is well suited for situations where brazing is not an option and hardfacing is too slow. Ferobide is typically used on seed drills, subsoilers, cultivators, ploughs, muck spreaders, root harvesters, sugar cane harvesters, buckets, mowers, augers, and scrapers.
One ideal placement is behind a brazed carbide edge, however if Ferobide is placed anywhere with sliding wear or in areas that avoid the impact of leading edges, results have demonstrated the effectiveness of Ferobide.
New developments in Ferobide have increased the impact resistance for leading edges however please avoid using standard Ferobide tiles on leading edges and points where the Ferobide is subject to heavy direct impact. Ferobide has been specially developed for excellent sliding wear performance and should only be used on leading edges with minimal impact.
Where welding is the only option for Ferobide, please enquire directly about our leading-edge solutions.
Ferobide is not to be used in above ground high speed applications, e.g. toppers, hedge flails, etc.
Ferobide is the most durable welded material readily available on the market and has upto 10x performance versus hardfacing, and up to 6x performance versus chocky blocks. Brazed pure tungsten has a slightly better wear resistance than Ferobide and while Ferobide is comparable to brazed carbide, Ferobide is slightly less durable. Brazed carbide is the best option for leading edges.
When used for the correct applications, Ferobide users can achieve a much greater working life and performance from wearing metal parts. As well as increased service life, Ferobide also helps to reduce downtime and save time & money on-farm.
Availability
To suit pipe sizes 15-169mm (PVC, HDPE, Copper, Steel)
Materials
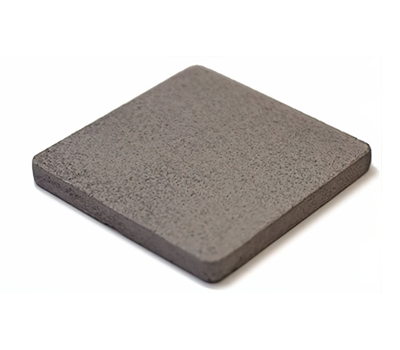
Resources
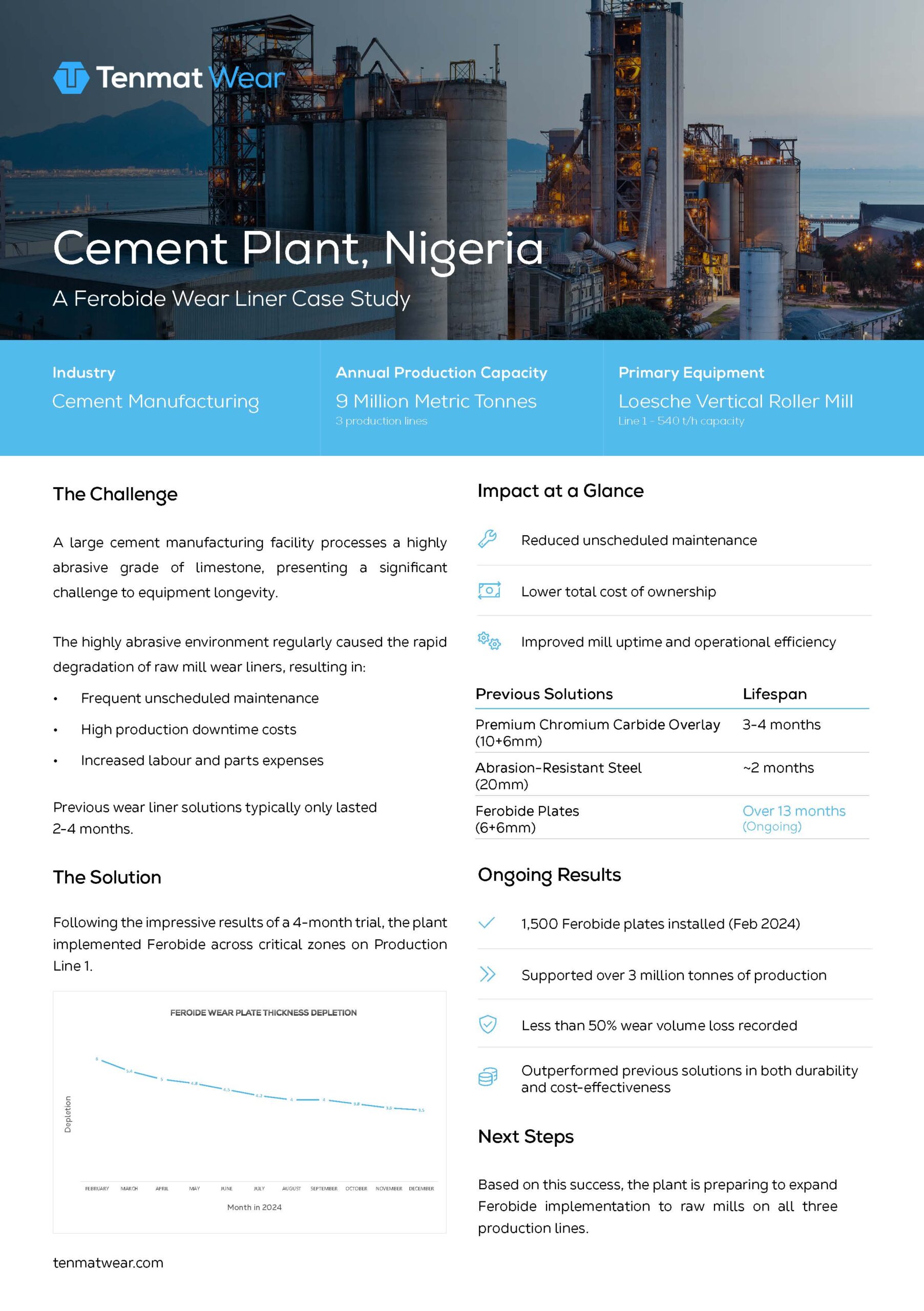
Contents
Nigerian cement plant faced rapid wear from highly abrasive limestone
Ferobide lasted 13+ months vs. 2–4 months with previous liners
Enabled 3M+ tonnes production with under 50% wear
Impressive performance driving expansion across all production lines